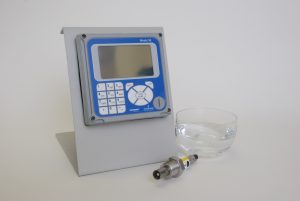
Water used in boiler feed should be as pure as possible. Boiler water contacts boiler heat exchangers, pumps, valves, and associated piping. Water impurities like suspended or dissolved solids or dissolved gases produce negative effects within the system. In order to understand the process better, water treatment specialists use grab sample testing methods or online pH, conductivity, TDS (total dissolved solids), and dissolved oxygen instrumentation. Knowing this, they can design a program for external or internal boiler water treatment. These include water softening, deaeration, membrane contractors, oxygen scavengers, anti-foaming, anti-priming, and others.
Here’s a brief summary of where conductivity measurement is used to help determine potential challenges to boiler water treatment. These include: scaling, oxygen and acid corrosion, and boiler water carryover such as foaming and priming.
Scaling
Scaling can plug piping over time, damaging pumps and boilers themselves. During the steam generating process, deposits from minerals in the water build up on the inside surfaces of system plumbing and equipment. Scaling buildup on metal surfaces reduces heat transfer within the boiler itself, making it more costly to power. The whole system becomes less efficient, and, in some cases, dangerous.
In order to prevent buildup, corrective action can be taken. As scaling increases, the conductivity of the water increases. To determine the extent of scaling, making a conductivity measurement with a continuous online conductivity monitor is recommended. A high temperature inline sensor is inserted directly into the process, or side steam that uses a sample cooler to reduce temperature, before the water reaches the sensor(s).
Foaming And Priming
Steam contaminated with boiler water solids produces two types of carryover: foaming and priming. Foaming is a bubble build up on the surface of the boiler water that passes out with the steam. It is caused by high concentration of any solids in the boiler water. Priming consists of droplets of water in the steam. This lowers energy efficiency of the steam and can result in salt crystal deposits on the boiler equipment. These effects can be measured with conductivity and TDS.
Oxygen Effect
Without proper mechanical and chemical deaeration, oxygen in the feedwater will enter the boiler. The oxygen that does not get flashed off with the steam will attack boiler metal, producing pitting. Also, water containing ammonia, particularly in the presence of oxygen, attacks copper and copper bearing alloys. The resulting corrosion can, in time, cause tubes to fail. Both an increase in dissolved oxygen and in dissolved solids from the corrosion are measureable.
Acid Corrosion
Low pH in feedwater as well as measurable, high conductivity resulting from contamination in water with pH lower than 8.5 will also produce corrosion. Both pH & conductivity measurement is used to control the extent of acid neutralization.
Caustic Corrosion
High caustic (NaOH) concentration can result from porous metal oxide deposits on tube metal surfaces or steam blanketing. Steam blanketing allows salts to concentrate on boiler metal surfaces. A steam layer forms between the boiler water and the tube wall, causing an inefficient heat transfer. Water that is rapidly vaporized will leave a concentrated caustic solution. Both conditions result in corrosive solutions that have measurable conductivity.
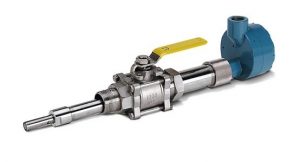
Putting a Conductivity Solution Together
A reliable conductivity motoring and control system consists of a sensor(s), mounting hardware or flowcell, conductivity transmitter, interconnect cable, and sometimes high-temperature junction box(es). Selecting the correct systems begins with identifying requirements in four areas:
- Conductivity Range
- Temperature
- Pressure
- Mounting
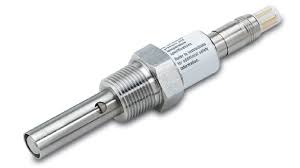
Contacting Conductivity Sensors are designed to use in clean water, low conductivity applications below 1000 mS. Most contacting conductivity sensors consist of two metal electrodes that come in direct contact with the process. An electrical field created between the sensor electrodes changes in proprtion to the conductivity of the process.
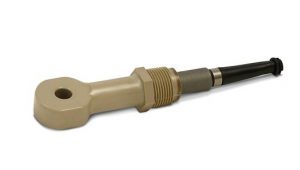
Toroidal Conductivity Sensors consist of two small electromagnetic coils (driver and receiver) encased in a plastic coating that isolates them from the process. The sensors can be used in solutions that can corrode metal electrodes. They’re designed for use in thick, sticky, gooey, or sludgy applications with conductivities above 200μS. The coils generate a measurable induction field that changes in proportion to the amount of conductivity in the liquid. As long as something doesn’t plug the center hole (it takes a lot!) these sensors will keep on working.
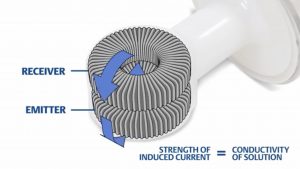
Troubleshooting Tip
More often than not, conductivity sensors are the workhorses of water quality instrumentation. They are more stabile, more robust, and longer lasting than pH, ORP, dissolved oxygen or other measurements. Every so often, however, they will produce erratic readings. From our experience, it’s temperature related – 90% of the time! Maybe a process upset burned out the the sensor’s built-in temperature compensation, or something happened to the wiring. Start with these. It will save you a lot of time.
Want to extend the life of your conductivity sensors in a harsh environment? Consider using a sample condition system that includes a sample cooler. Sample Coolers reduce the effects of temperature swings by allowing the conductivity sensor to remain in a more stabile condition. This will also extend sensor life.